Addihive
Additive manufacturing, or 3D printing as it is more popularly known, has the potential to revolutionise current manufacturing practice. Complex devices with multiple moving parts can be made in a single process with no further assembly required. It also opens up the prospect of truly personalised manufacture of devices such as prosthetics, artificial heart valves and so on.
Despite this potential and clear advantages over traditional processes the rate of adoption of the technology has been slow, to say the least. "It's been a lot slower that expected," says Patrick Byrnes, research and development manager with Addihive, which is based in Co Limerick. "A lot of the equipment being supplied at the moment is more suited to an R&D setting than a manufacturing environment."
Addihive was established to address this issue by providing solutions to some of the constraints which have affected metallic additive manufacturing up until now.
“Addihive enables serial additive manufacturing in highly-regulated aerospace and medical device industries through market leading innovative solutions,” Byrnes adds. “Additive manufacturing or 3D printing in metals is disrupting these global market segments at an accelerating pace where new approaches and engineering challenges are presented for part quality, system validation and process control.”
One of these challenges arises in the sphere of health and safety. “When you are moving metallic particles around at high velocity in a confined space it is like a grain silo and particles can ignite,” he says.
There are also issues with material handling and wastage. The metals involved are very high value and even more losses can be very costly. Furthermore, with individual additive manufacturing machines costing up to €1 million each, efficiency is at a premium.
Powderloop
Addihive has created a technology solution known as Powderloop which sits on top of the manufacturing unit monitoring the process through all its stages, collecting metal particles for recycling and monitoring levels of oxygen, nitrogen and hydrogen in the system to ensure chemical integrity.
“Our mission is to streamline, complement and scale the additive process with our customer base through the implementation of proprietary technology and market-leading solutions,” says Byrnes. “We have been in operation since January 2017 with a team of three engineers and, to date, we have developed a number of patent-pending innovations across pre- and post-processing platforms. We had seen a relatively strong push on the marketing and uptake in additive manufacturing equipment with multinational customers, but nobody seemed to cater for the pre- and post-process ecosystem and we created a number of innovations to exponentially improve environmental health and safety, overall equipment efficiency and process quality.”
In short, the Powderloop technology makes the additive manufacturing process quicker, cheaper, cleaner and safer. “Our vision is to accelerate the uptake of additive manufacturing and disruptive technologies from SMEs right through to multinationals,” Byrnes adds.
Innopharma
Modified drug release rates play a key role in the efficacy of modern medicines. For example, delayed release of active ingredients allows patients to take fewer tablets or capsules to achieve the same benefits. This is achieved through the coating which is applied to the drugs. Not the coating on exterior shell of the tablet but the one applied to the individual particles of the active ingredient contained inside the tablet or capsule.
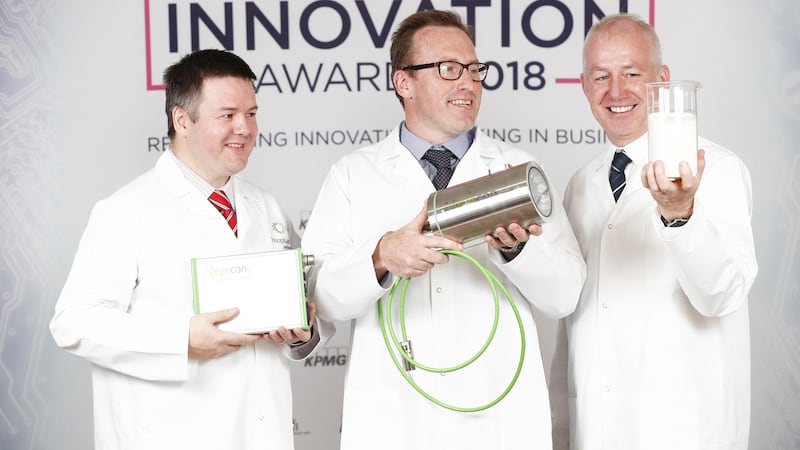
These coatings are applied using a process known as fluid-bed coating. However, currently there is no smart means of controlling the coating thickness of the active pharmaceutical ingredient during the application process. This can lead to variations in thicknesses, causing entire batches of pharmaceuticals to be rejected as a result.
Innopharma has developed a solution to this issue which incorporates Internet of Things technologies such as smart sensors, data feeds and real-time data visualisations to track and control the coating process. The solution ensures the very specific coating to establish the drug release profile for a given batch of capsules or tablets is achieved. It allows pharma companies to manufacture a batch of drugs with a precise coating thickness in the shortest possible time and delivers a full record of the operation.
Growing demand
“Our technology allows pharmaceutical companies to control the coating process and ensures each batch is within specifications,” says Seán Costello, technical operations director with Innopharma. “The other part of the story is the growing demand for modified-release drugs. Using traditional drugs a patient might have had to take a tablet or a capsule four times a day or more. Using modified-release drugs, they can have a 24-hour dosage in one tablet. This aids patient compliance and makes it much easier for them to take their medication on time every time.”
Another side of it is the reformulation of existing medicines for other uses and applications. “Adult medications can be reformulated and made suitable for the paediatric market,” Costello explains. “It will also be possible to combine more than one medicine in a single tablet, again improving compliance.”
The Innopharma solution uses sensors to video the process at ultra-high resolution and then uses advanced image analysis software to track the coating of the particles. “The images are analysed in real time with the results sent directly to the process equipment,” Costello adds. “This allows parameters to be changed in order to keep the process on track. The system adapts dynamically to deliver the right results every time.”
The technology was launched in late 2017 and the company is currently engaging with potential customers and partners in the global pharmaceutical industry. "We are actively promoting and marketing the technology at present and we have set up a demonstration laboratory at our head office in Sandyford in Dublin where customers can come and see it in action. We are also working closely with fluid-bed coating materials manufacturers to leverage access to the market for our value proposition to customers."
Marco Beverage Systems
The rapid proliferation of speciality tea and coffee shops has led to a particular technological challenge. Not all teas are created equal and different blends need to be made with water at different temperatures for the best results. This has led to coffee shops installing two or three separate boilers on their countertops or under them – taking up valuable space and adding considerably to costs.
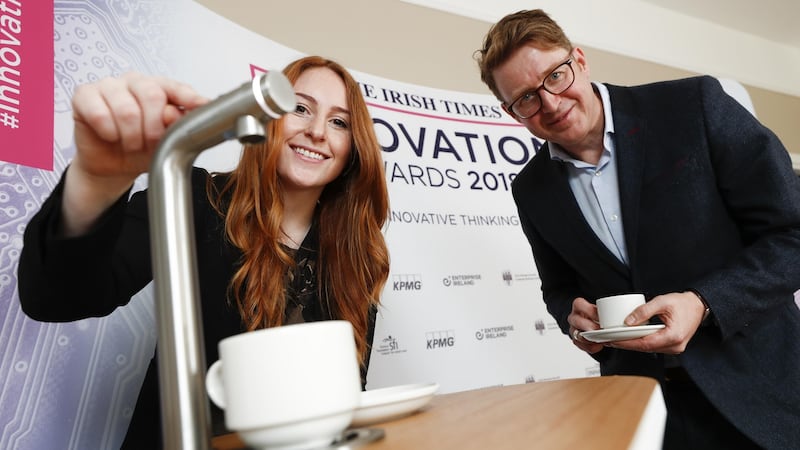
Dublin company Marco Beverage Systems has come up with an ingenious solution in the form of the Mix – a boiler system which delivers water at three different precise temperatures.
"We have been manufacturing hot water systems for more than 30 years," says operations director Paul Stack. "They have mainly been used for black tea and coffee, but the trend now is towards speciality teas and other drinks. Black tea should be made at a temperature a little below boiling, around 96 degrees or above. Filter coffee should be made at between 92 and 96 degrees, while green tea requires water in the mid-80s. This involved the use of a lot of different pieces of equipment."
The Mix utilises a single boiler and an innovative mixing system which takes high-temperature water and combines it with cold water to provide water at a precise preset temperature. The machine can deliver water at three different temperatures at the touch of a button.
Energy efficiency
Another advantage of the device is its energy efficiency. “We have taken the principle of the Thermos flask and applied it to the Mix,” Stack explains. “It has a double-walled vacuum-insulated tank which almost eliminates heat loss. The Mix is 66 per cent more energy efficient than its top five competitors. One of our US customers will save $100 (€87) a year in energy costs per machine. We estimate it could save them $4 million over five years across their 8,500 outlets.”
The product has been very well received on the market since its launch in 2017, not least for its aesthetic qualities. “It is beautifully designed,” Stack points out. “The boiler is moved under the counter with the water dispensed through a stylish and space-saving fount. Customers come into the shops for the overall experience and this allows staff to spend time talking to them rather than turning their backs on them while dispensing water.”
Market response has been very positive since its launch in 2017. "About 86 per cent of our sales are to export markets – 40 per cent to the UK, and the rest divided between the US, Europe and the rest of the world. The Mix already accounts for 10 per cent of our business and is growing strongly. Starbucks has specified it for their Starbucks Reserve concept. This will have a hero effect and will help with global sales. It also cements our reputation for the development of innovative beverage systems."