The State’s first certified container house is a unique home that appears both alien and entirely of its place.
At first glance, it might look to be nothing more than an overfill storage space for one of the shipping companies that bring containers to the docklands from every corner of the world. In fact, there is a link. The seven containers in situ on Fitzwilliam Street, Ringsend, were sourced nearby, off Pigeon House Road, among the city of containers that frame the southern mouth of the Liffey.
However, these containers' days of shipping freight from China are over. They now carry a much more precious cargo – a family of four, the Kelleys: Gordon, Maggie, Gordie and new arrival Penny Bell.
0 of 4
We had no a clue what we were going to build and we didn't have any money left. Maggie suggested that we should just live in a shipping container on the site and I loved the idea.
It's the shot-blast treatment of the external walls that reveal the first sense of warmth about the structure. The finish was inspired by the work of Richard Serra, the American minimalist sculptor renowned for his work with sheet metal and his large scale site-specific structures.
Next to catch the eye are the multiple full-length doors of glass on both floors of the street-front exterior, reflecting the once grand Regal Cinema’s Art Deco facade on the opposite side of the street. Finally, the negative entrance space created by one overhanging second floor container simply invites you in.
Extreme minimalist
Retaining the essence of the containers’ original feel and external finish was core to the Kelleys’ vision. The interior finish is extreme minimalist but resembles any modern home with a similar style predilection. The ground floor features an open-plan kitchen and dining room that will also be the family’s living space until the build is fully complete.
The second floor is accessed via a plywood square spiral staircase; this smart and functional space-saving design acts as a neat metaphor for the entire build.
As you enter the three-bedroom second floor, you completely forget you are in a container house. It’s impossible to appreciate the orientation of the containers or where they start or finish. When finally added, the four-container third floor will be an open-plan living space complete with a living sedum roof garden.
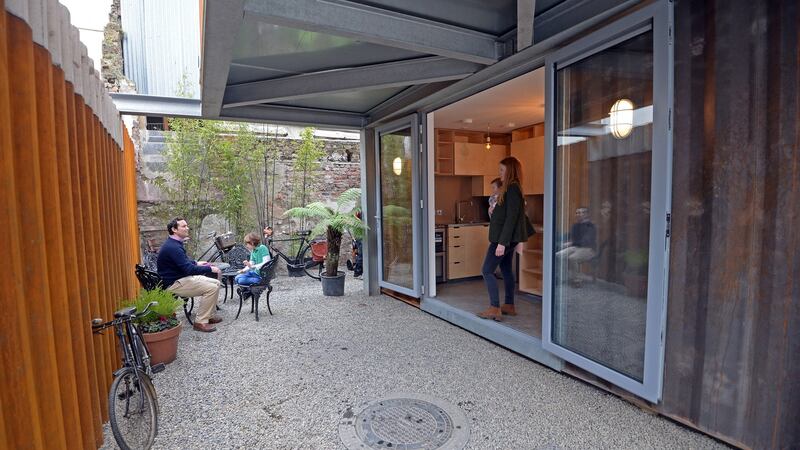
The reason the Kelleys are moving into their home minus one floor is down to access to finance. While the planners loved their pioneering 11-container house design and concept, the banks would not touch it.
“They said it was just too unconventional,” says Gordon Kelley. “I tried every bank and the story was the same. Our only option was a save and phase-build process.”
A container house of this nature isn’t as cheap as many might think. To complete the ground work and the two floors to date has cost the Kelleys €300,000. The site was purchased for just under €50,000. Had all the finance been in place from the get-go. the six-month build and costs could have been reduced as all fabrication could have been done offsite and the finished containers simply craned into place.
The single trip high-cube containers used are also more expensive than standard container: €3,000 each as opposed to €1,500, because they are harder to come by. (The benefit is the regulation ceiling height.) The Kelleys are now saving towards the €75,000 needed to complete the third and final floor of their home.
Serious expense
According to their builder, PJ McGann, a more conventional approach on a site like this could have cost twice the money.
“You wouldn’t be able to build a standard house on Gordon’s site for starters,” he says. “The ground conditions are poor; so much of Ringsend is reclaimed. He has boundaries with about six properties. He’s got fire considerations. Space is tight. You’d have to use a commercial structure with lots of steel and glass and then you’re into serious construction expense.
“When the third floor is added, Gordon will have a 158sq m home on a 70sq meter site. That’s a phenomenal return for a pretty low cost, relative to the alternative options on a similar site in that area. It could cost double.”
The modular nature of a container build also makes it easier to occupy a partially completed home in a way that a conventional house never could, says Matthew Beattie, one of LiD Architecture's three-strong team to work on the project, along with Deirdre McMenamin and Dougal Sheridan.
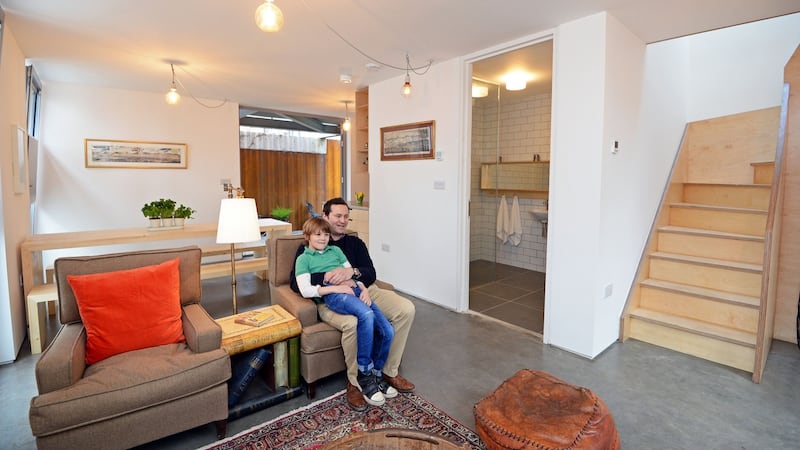
“Containers lend themselves more to a modular or phased build relative to any other kind of project I can imagine,” he says. “ It’s going to be quite simple to finish Gordon and Maggie’s house as per the original three-storey concept when the time comes.”
The flip side is the design rigidity of the material in their raw form.
“Structurally, they do come with limiting constraints,” Beattie says. “The container wants to do its very simple job in its most efficient way. As soon as you start chopping them up, you compromise their integrity. If you start adding steel, for example, all the reasons you choose containers – such as cost-effectiveness and the sustainability argument of using materials that already exist – you start to lose that.”
Vacant site
The idea first came to the Kelleys more by chance than design, when they spotted the ramshackle vacant site for sale in 2010. Gordon, an avid sailor and member of the nearby Poolbeg Sailing Club, had a real affinity for the area; he and Maggie always felt it was a part of the city they could call home.
“It was a blind bid and we put all our savings on it,” he says. “ We won, but we had no a clue what we were going to build and we didn’t have any money left. Maggie suggested that we should just live in a shipping container on the site and I loved the idea. It fitted perfectly with the vernacular of Ringsend and the docklands location.”
The Kelleys weren't the first to conclude that shipping containers present an opportunity to add to the aesthetic and vernacular of the docklands area. In 2009, LiD Architecture submitted the winning design for a proposed new civic space, Dublin Parlour, in that locale. The concept called for 125 shipping containers to create a temporary space between the 3Arena and the Gibson Hotel.
The economic crash put paid to the project just before going to tender, but during his research Gordon came across the plans – and they resonated.
Two parts of the container house jigsaw were in place. The third was Buildstruct JP McGann Ltd, the company recommended by the engineer for its specialisation in steel fabrication and ability to take on builds from the more interesting end of the spectrum.
"They were getting crazy quotes for the job," says McGann. "I think, number one, because people probably weren't interested in doing the job, and number two, because they didn't understand it. We wanted to make sure we did the best job we possibly could as this was the first time it was ever done in the Republic of Ireland. "
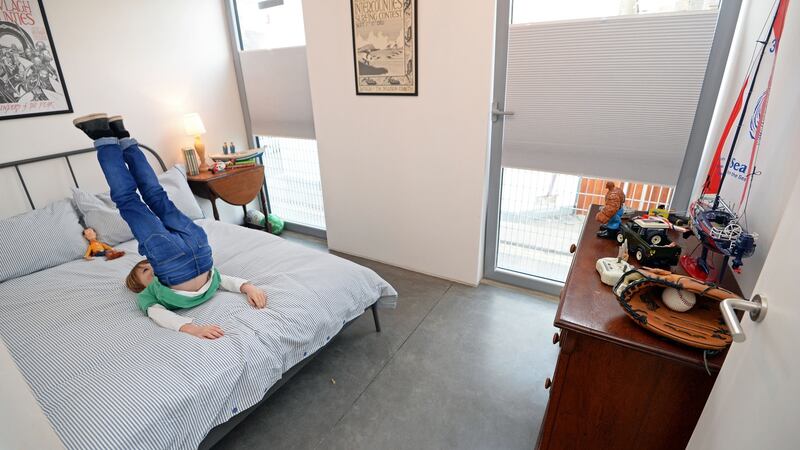
One other such home featuring a single 40sq ft container was known as Project Ripple and built on the grounds of Dublin's Irish Museum of Modern Art in in 2014. A project of social change facilitator and author Carol Tallon, Project Ripple aimed to come up with a low-cost model of housing in the aftermath of the property crash. The innovative, movable end product featured voluntary contributions from 65 professionals and trades people and is now in situ in Cork city.
While believed to be Ireland’s first building-compliant container house, Project Ripple was not certified to all construction standards, unlike the Kelleys’. The Ripple container home, which was granted planning permission by Longford CC, is utilised as an emergency housing unit and is part of the St Vincent De Paul facility in Longford town. The unit has been up and running for nearly two years and has housed some 15 people on short-term occupancy. While not approved for long-term occupation, the Ripple home is fully certified with the Building Regulations and meets the construction standards for a domestic home.
The Kelley’s build had an overriding design and brief, but there was no roadmap for the multiple nuances that arose along the way. Owners, architects and builder alike acknowledge the amount of creative problem-solving and flexibility required to achieve the optimal end result.
For example, the entire internal skin of the structure was sprayed with a coating of closed-cell polyurethane foam, leaving it completely airtight and insulated. This also added significant mass to the structure. (When walking on the roof of a standard container, there is some give/bounce. After this treatment, roof feels completely solid). A plasterboard finish allows for a traditional interior wall surface.
Condensation risk
This highly effective and efficient approach differs from the more accepted method of finishing a container for residential purposes: using a timber stud drylined with insulation. The latter, McGann warns, runs the risk of condensation should any air get in. A 20-mill sheet of heavy-duty plywood covered by insulation layers the internal floors. On top of this lies the underfloor heating with a final concrete surface finish.
Both Beattie and McGann say containers are not for everyone. They are also effusive in their praise of the Kelleys for bringing this pioneering project to fruition despite the numerous challenges and a lack of any blueprint. When the family walked into their new home this New Year, it was the first container house they had ever been in, let alone called their home.
If that isn’t thinking outside the box, I don’t know what is.