A new sea ferry built using carbon fibre, wind turbine blades manufactured using recycled plastics, lighter and more fuel-efficient aircraft, and life-saving critical care equipment for Covid-19 patients. These are just a few of the breakthroughs which have come about through the work of composite materials researchers at Ulster University
Working in collaboration with leading companies in renewable energy, health and life sciences, automotive, marine, aerospace, and advanced manufacturing sectors, Ulster University researchers have helped develop new patented technologies and achieve significant cost and performance improvements in manufacturing. They have also delivered on-site industrial training, assisted with new material and process integration, and supported the success of a growing number of spin-out companies.
“We have a very strong aerospace industry in Northern Ireland,” says Dr Edward Archer, senior lecturer in advanced composite materials at the Ulster University School of Engineering. “We have been working in close collaboration for many years and have been bringing the same skills and techniques to bear in other areas like advanced manufacturing and the automotive industry. We are also very excited about the renewable energy and marine sectors.”
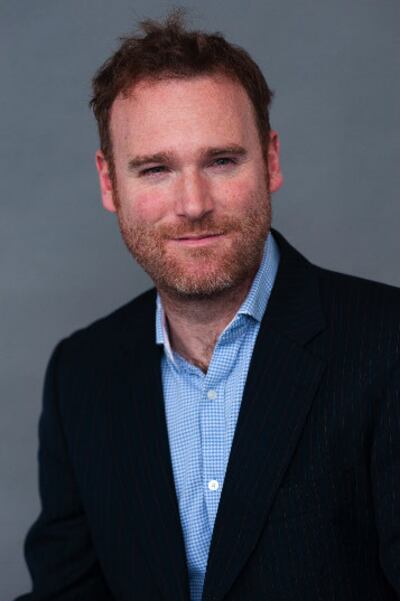
Indeed, the use of advanced composite materials could see large scale shipbuilding return to Belfast. Ulster University is currently part of the Belfast Maritime Consortium which is led by former Americas Cup yacht race participant Artemis Technologies. The university is bringing its skills and knowledge in textiles and composite fibres to the project.
“They are bringing technology from that arena to commercial sailing, and they are going to use carbon fibre to build ferries in Belfast,” says Archer. “The consortium is funded by the UK government. It might seem high risk in some ways, but the Artemis team knows what it’s doing. Their project manager is a former technology officer for the Red Bull and Williams formula one racing teams. It’s fantastic to see that combination of skills coming together in this way.”
This project is strongly associated with the university’s expertise in textiles. “This developed from ancestral Ulster weaving technology and we have now applied it to higher end engineering sectors. We are working with companies like Artemis and others in the aerospace and automotive sectors to develop advanced textile composites to meet industry needs.”
Links to the renewable energy sector go back almost two decades. “We started working with Galway company EireComposites back in 2002,” says professor of advanced materials, Alistair McIlhagger. “The company is a spinout from NUI Galway and we began collaborating with them on a cross border funded project which looked at the design and manufacture of wind turbine blades. We worked on a 12.5 metre demonstrator blade manufactured from recycled plastic materials and we have continued to work with them since then.”

That led to an EU Seventh Framework research grant to develop marine turbine blades 10 years ago. “We moved from wind to the marine,” McIlhagger adds. “The partner chosen to build the demonstrator was Harland and Wolff and we also had other partners in Scotland and Europe. That was a very good project to start us off in marine materials like the ones which will be used to build ferries. Our work on marine turbines continues today.”
These are just two examples of the transferability of the technologies produced by the Ulster University team. “What we’ve really looked at over the years is bringing multi-disciplinary research activity to look at novel technologies and products to provide robust, cost effective and environmentally sustainable solutions. What we find is that by having that fundamental materials understanding and underpinning scientific and engineering knowledge we are able to transfer the technologies into different industries like the marine, renewable energy, aerospace, mass transit and others. We are enabling companies to avail of these technologies and acquire new skillsets. By working closely with companies, we are able to understand what industry needs are now and into the future so we can provide the skills they require. That puts us in a position to train people to have the skillsets that will make those companies more profitable.”
We enjoy the best of both worlds in Northern Ireland in that we are still able to tap into EU and UK funding streams
Most recently, that approach has seen a move into the life and health sciences sector. This arose through the university’s participation in the Northern Ireland Advanced Composites and Engineering (NIACE) research centre. “This is our flagship collaborative research centre,” says Archer. “We have co-located equipment and industry partners and the two universities, ourselves and Queens, there. It is an industrially-led, university facilitated centre and its purpose is to produce industry leading research projects. It brings together engineering companies and knowledge providers to work on projects developing technical expertise and helping support innovation and product development for the benefit of the Northern Ireland economy.”
According to McIlhagger, life and health sciences was new to the composites research group but not for the university. “Some of the novel materials we have been working on are now really helping in this area. For example, we collaborated with Armstrong Medical on using a new permeable polymer material to make a breathable tube for patients in critical care. This improved the performance of the tubes as they don’t suffer from the condensation issues associated with other models and don’t have to be checked as often. This reduced the workload of staff in ICU departments. The technology can also be adapted for paediatric and neonatal care. It’s been amazing to see the same skillsets and technology used to make aircraft more efficient being utilised to improve patient care.”
Archer describes the project as revelatory. “It has opened our eyes to what can be done. An EU funded project led us to this. Our team has grown at Ulster University and the new staff coming in brought new skills with them. This led us into the health and life sciences sector. It’s great to see our technologies being used to improve the world. In some ways it’s more tangible than a plane or a ship.”
Some of the other staff and partners in NIACE became involved in the printing of PPE at the early stages of the pandemic, according to McIlhagger. “Denroy Plastics is involved in the aerospace sector and also manufactures components for hairbrushes,” he notes. “When the call came to tool up to make PPE they answered the call very quickly. They also designed some new face mask equipment and turned that into a new product line.”
That link between linen and life sciences is very powerful. “The underlying science is very similar,” says McIlhagger. “When you pin it down, it’s a polymeric material which can be reinforced with high performance fibre. When you understand it for one industrial application you can hopefully apply it to others.”
And Archer and McIlhagger want new companies and partners to come and collaborate with them on research projects. “We definitely want new partners and companies of all sizes to join us,” says Archer.
“There is funding available that can be tapped into. We enjoy the best of both worlds in Northern Ireland in that we are still able to tap into EU and UK funding streams. That is very important in supporting us as we try to address global issues and work with partners in Ireland, the UK, Europe and further afield. Many of our partners are multinational firms and they want to work with international partners. We also work with a large number of SMEs in Northern Ireland and we are helping them to become agile and pivot their businesses into new areas as opportunities arise.”
Archer and McIlhagger formed Axis Composites Ltd in 2010 which undertakes industrial-scale prototyping of complex 3D woven structures and has been working across these various industrial sectors.
[ For more information visit ulster.ac.ukOpens in new window ]