Kyran O’Grady works in a craft that dates back nearly 5,000 years, one of the oldest forms of roofing in the world and once a familiar feature of the Irish rural landscape. Based in Wicklow, he has thatched everything from cottages and houses to pubs and offices and has even recreated Viking and Iron Age dwellings from archaeological drawings. He harvests his own reeds in Wexford and has designed and made his own machine – in tandem with another thatcher who is a steel fabricator – for cleaning, raking and making the bundles necessary for his work.
From Howth and a family involved in the clothing business with no tradition of thatching, O’Grady remembers being fascinated and intrigued by thatched houses on holidays in Sligo as a child and later, after a commerce degree, toying with ideas of buying and renovating old buildings.
"Then the opportunity came along to do a six-month thatching course with Anco in 1981 around Ardara and Portnoo in Donegal – there were around 12 of us on the course and we worked on six or seven houses.
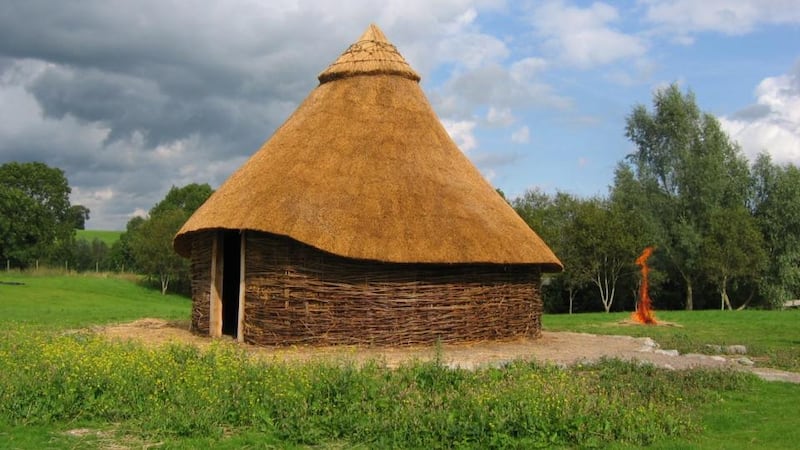
“After that I worked with a master thatcher in a huge house on the way into Strabane which had a lot of windows, valleys and hips, so I got thrown in at the deep end,” he recalls with a smile.
Thatched roof and outhouses
It’s not hard to spot his house up a country laneway not far from Wicklow town with its thatched roof and outhouses, heavy machinery sitting alongside a yacht and mast (he’s a keen sailor) and a devoted Rottweiler demanding attention. O’Grady moved there in the 1980s so he could cut his own reed, a job that takes up the first three months of the year. Reeds grow to 6-7 feet and are fully grown in a year, he explains, adding that beds are found mostly in Wexford, Youghal and river estuaries.
Why do people want thatch, which is three to four times more expensive than a slated roof and requires more upkeep? “They are fascinated by its aesthetic beauty and there are those who have always wanted it,” he says, adding that many environmentalists who would love thatch can’t afford it. Thatching an Irish cottage costs around €10,000-€20,000 and takes a month to two months to complete.
“A thatched roof is warm and there is nothing more sustainable, with completely natural materials that take in carbon as they grow. It doesn’t need gutters and is one of the best insulating roofs you can get,” he says. Maintenance normally involves re-ridging every 8-10 years. Ridges can be plain block style or ornamental and he considers Dunmore East to be Ireland’s prettiest village with a lot of thatch “and planning controls are very good and they preserve and encourage people to thatch”.
But what about fire? Today’s regulations demand a fire barrier underneath the thatch and on top of the rafters “so that the building can burn for an hour before it will affect the roof and the roof can burn for an hour before it affects the building”, he says.
One of his first major projects was roofing the Orchard pub in Stillorgan in the mid 1980s. “It was a big roof, 6,500sq ft needing 6,500 bundles, three 40ft containers and it took three to four months to complete,” he recalls. The Orchard set a trend around the country with a succession of pubs following in its wake such as Glenside near Nutgrove, the Lord Mayors in Swords, the Playwright in Blackrock, Courtneys in Lucan and a few others around the country.
‘No overweight thatchers’
Other projects included thatching 10 vacation cottages on Cruit Island in Donegal for Rosses Point schoolteacher Conor Ward, Noel Keating’s Kepak offices in Clonee and Bunclody Golf Club. One unusual job was covering a car park in Kilternan Sports Hotel for the late Hugh O’Regan that took almost three acres of willow to finish. O’Grady reckons it is the biggest willow wall in the world. Another challenge was recreating an Iron Age circular willow and reed thatch building in Armagh at Navan Fort.
There are three or four different types of thatch, he points out, reed being just one of them. As a reed thatcher, O Grady’s primary tool is the legget, a spade-like instrument that dresses the reed into position.
The first bundle forms the eave of the roof and the thatcher starts his work on standard rafters running a course in rows of bundles that are tied with binder twine or screw fixed into position with stainless steel wire.
“Traditionally they were held with scallops – pieces of willow or hazel which end up like a staple,” O’Grady explains. “Each course brings you up about 18.” The process is slow and the hardest part of thatching is patience, he says.
It is not without its hazards. Ten years ago he broke both heels stepping off scaffolding after spraying a roof he had just finished and ended up in a wheelchair for six months.
“The nature of the work is very physical – there are no overweight thatchers,” he says with a grin. Now, for the next three months he will be cutting reed and will then head north to Aughnacloy to a house he thatched 25 years ago to put on a new ridge, then it’s back to Bunclody for more ridgework “and then I’ll be waiting for the phone to ring”.