For over a century, Mitsubishi Electric has been dedicated to continuous technological innovation and ceaseless creativity. Today, this translates into a focus on developing solutions that address the social and environmental challenges facing the world. Sustainable products are a crucial component of that effort.
“Our products are designed with a focus on minimising their impact on the planet throughout their entire life cycle, from sourcing raw materials responsibly to reducing energy consumption during production,” says Margaret Rafter, consultant sales engineer with Mitsubishi Electric. “At Mitsubishi Electric we bring technology and products to the market that help homes, business, and industry heat, cool, ventilate and automate in a more energy efficient way. This reduces their impact on the environment. We want to take things one step further by integrating and harmonising our diverse range of products to create even more efficiencies as we strive to build a more sustainable future for us all.”

The aim is to create a one-stop-shop where mechanical and electrical engineering clients can go to for their heating, ventilation, air conditioning, and automation needs, she explains. “A large part of my job is working with consultants to help them select and specify equipment for the projects they are working on,” she says. “They are under increasing pressure to deliver buildings that comply with new legislative standards on sustainability as well as voluntary green building standards that their clients want to apply. We help them to design near zero energy buildings (NZEB) by providing high performing and highly efficient equipment.”
Those voluntary green building certifications are growing in importance, she adds. “Clients want to go further than the regulatory requirements. They are not just selecting units for compliance with those regulations, they are striving for higher targets and better performance through standards like Leadership in Energy and Environmental Design (LEED) in the US and Building Research Establishment Environmental Assessment Method (BREEAM) in Europe. We help consultants and their clients to achieve those goals.”
The secret to cooking a delicious, fuss free Christmas turkey? You just need a little help
How LEO Digital for Business is helping to boost small business competitiveness
‘I have to believe that this situation is not forever’: stress mounts in homeless parents and children living in claustrophobic one-room accommodation
Unlocking the potential of your small business
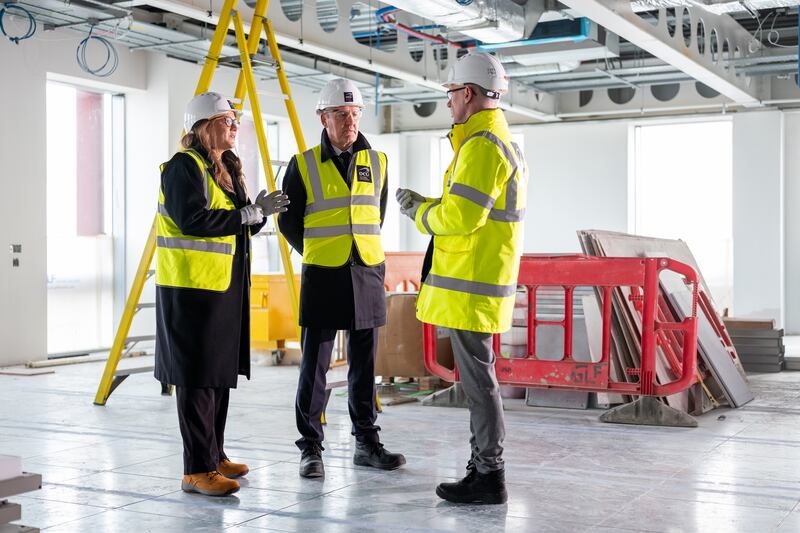
Sustainability is front of mind for all clients now, according to Stephen Walsh, joint managing director of JV Tierney & Co consulting engineers. “We do a lot of work accrediting buildings’ energy performance to BREEAM and LEED standards. This is important for companies’ ESG policies and matters more than ever to them. Sustainability is an easier conversation to have with clients now than it might have been a few years ago. They realise they have to come on board in relation to decarbonisation and addressing climate change. They are grasping the nettle.”
He points out that sustainability is now a feature of public works contracts. “The embodied carbon of buildings and their operational emissions now form part of contracts with Government departments,” he notes. “There has been a marked shift over the past 15 to 18 months and the majority of projects are now applying alternative energy sources for the provision of heating and hot water generation rather than fossil fuels, for example.”
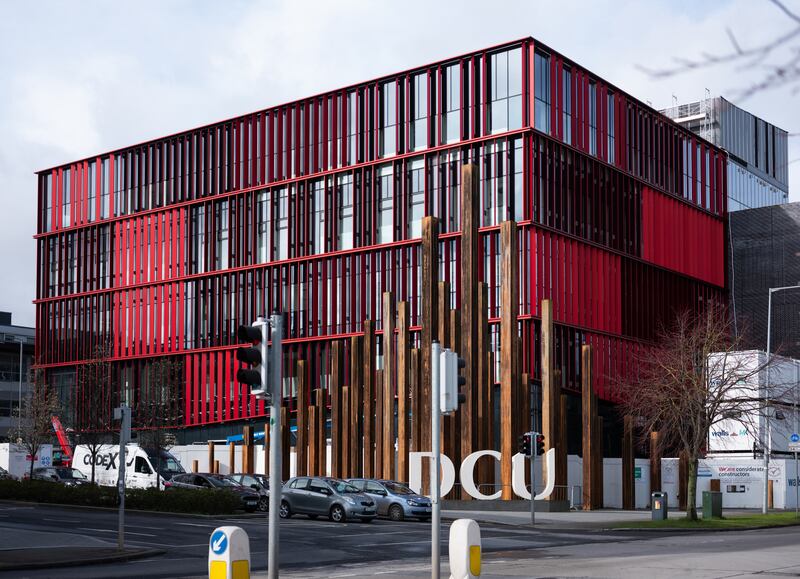
He has been working with Mitsubishi Electric on sustainability issues for quite some time. “I have had a very good relationship with Mitsubishi for more than 30 years and the firm has been working with them for a lot longer than that,” he says. “They are very good with respect to sustainability and invest in research & development for the future. For example, a lot of the equipment we specify has refrigerant gases in it. These gases have ozone depletion numbers, the higher the number the worse the impact on the ozone layer. Mitsubishi is making the units more environmentally friendly and have introduced a hybrid variable refrigerant system with the refrigerant mainly confined to the external elements of the system while the interior element contains mainly water. This reduces the amount of refrigerant required and is much better for the environment and supports decarbonisation efforts.”

It is not just about products, however. Mitsubishi Electric is on hand to provide advice and guidance. “As design engineers, we need to be in advance of the curve about what’s coming down the line both in terms of new regulations and standards and products coming on to the market,” he explains. “The capital projects that we are involved in can typically take five or six years from initial design stage to handover. You don’t want to have to make alterations to the design during the process because of legislative or updates to standards or directives. We have to constantly probe the horizon. Mitsubishi is great at that. They keep us updated on where they are going with new product development and let us know about their R&D activities.”
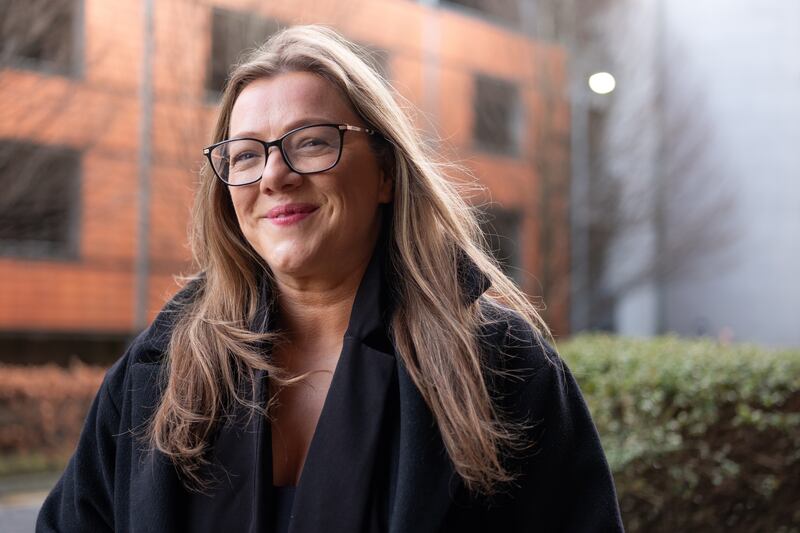
Mitsubishi is also able to bring its own experience of projects to bear, according to Margaret Rafter. “Sometimes a consultant looks at a project and might need a different solution. It could be an office building for an organisation with a lot of people working from home that doesn’t need systems running 100 per cent of the time. Heating, ventilation and air conditioning is responsible for a huge proportion of a building’s energy consumption – up to 40 per cent. So one of the ways we can reduce this is through tighter controls and the use of passive infrared sensors (PIR’s), that can detect the presence of people in a space. If no one is in the room the system switches off. This means the unit is only run when required. We can also use CO2 sensors in ventilation systems to activate the system when CO2 goes above a certain level, this allows the ventilation unit to ramp up and down in increments of 5 per cent, running the unit more efficiently ”
Efficiency gains also help. “Fans have changed significantly,” she notes. “In previous years we used backward curved belt driven fans, which had to be replaced quite often. Now we have electronically commutated fans which are easier to maintain and much more energy efficient. Higher efficiency filters also help. Heat pumps have also become much more efficient. To support consultants we are able to give them the datasheets and specifications to allow them to calculate the energy requirements of all our equipment. Also, by utilising the Mitsubishi Electric embodied carbon information database (EPDs and CIBSE TM65 calculations), project teams will be able to accurately account for the embodied carbon associated with their mechanical plant – which may be a requirement under legislation released in the near future.”

JV Tierney also works with Mitsubishi on the continuing professional development of its engineers. “Mitsubishi staff come in and talk to us about what’s coming down the line,” says Mr. Walsh. “We also go into their offices where they have mock-ups of their new technology. To be able to see that in the flesh is very helpful in getting a better understanding of it. Also, if ever we need someone to talk to about technical issues we can go to Mitsubishi Electric. They are very good for that and our relationship with them continues to grow.”
Find out more about the range of solutions at Mitsubishi Ireland here